Click to Expand
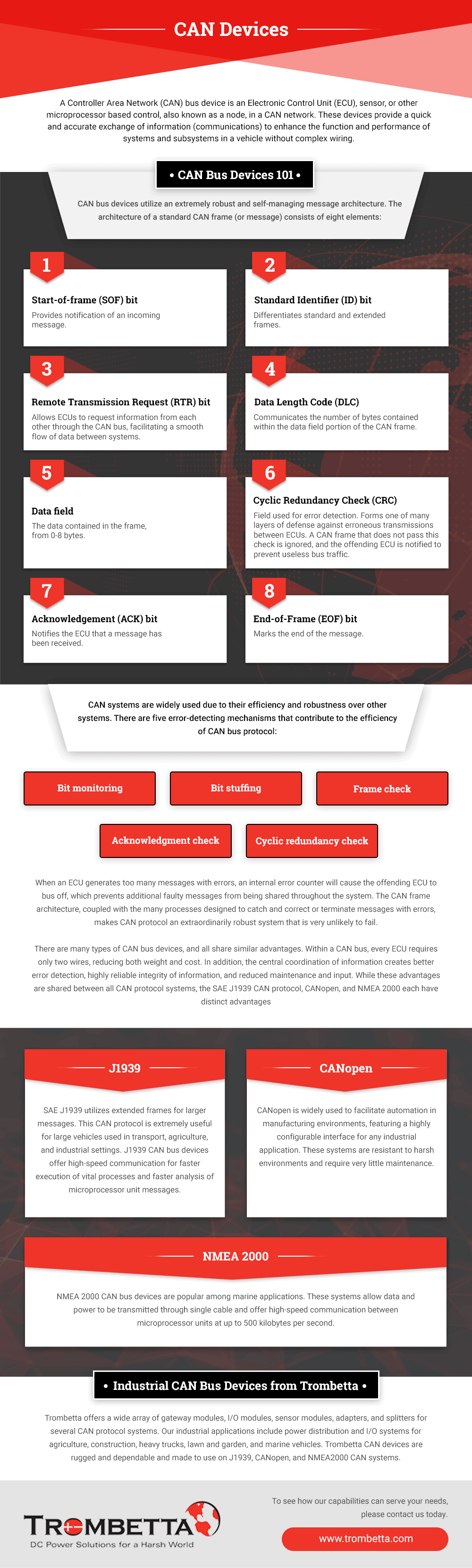
What is CAN?
A Controller Area Network (CAN) bus device is an Electronic Control Unit (ECU), sensor, or other microprocessor based control, also known as a node, in a CAN network. These devices provide a quick and accurate exchange of information (communications) to enhance the function and performance of systems and subsystems in a vehicle without complex wiring.
CAN Bus Devices 101
CAN bus devices utilize an extremely robust and self-managing message architecture. The architecture of a standard CAN frame (or message) consists of eight elements:
- Start-of-frame (SOF) bit — Provides notification of an incoming message.
- Standard Identifier (ID) bit — Differentiates standard and extended frames.
- Remote Transmission Request (RTR) bit – Allows ECUs to request information from each other through the CAN bus, facilitating a smooth flow of data between systems.
- Data Length Code (DLC) — Communicates the number of bytes contained within the data field portion of the CAN frame.
- Data field – The data contained in the frame, from 0-8 bytes.
- Cyclic Redundancy Check (CRC) — Field used for error detection. Forms one of many layers of defense against erroneous transmissions between ECUs. A CAN frame that does not pass this check is ignored, and the offending ECU is notified to prevent useless bus traffic.
- Acknowledgement (ACK) bit — Notifies the ECU that a message has been received.
- End-of-Frame (EOF) bit — Marks the end of the message.
CAN Bus systems are widely used due to their efficiency and robustness over other systems. There are five error-detecting mechanisms that contribute to the efficiency of CAN Bus protocol:
- Bit monitoring
- Bit stuffing
- Frame check
- Acknowledgment check
- Cyclic redundancy check
When an ECU generates too many messages with errors, an internal error counter will cause the offending ECU to bus off, which prevents additional faulty messages from being shared throughout the system. The CAN frame architecture, coupled with the many processes designed to catch and correct or terminate messages with errors, makes CAN protocol an extraordinarily robust system that is very unlikely to fail.
There are many types of CAN bus devices, and all share similar advantages. Within a CAN bus, every ECU requires only two wires, reducing both weight and cost. In addition, the central coordination of information creates better error detection, highly reliable integrity of information, and reduced maintenance and input. While these advantages are shared between all CAN protocol systems, the SAE J1939 CAN protocol, CANopen, and NMEA 2000 each have distinct advantages.
J1939
SAE J1939 utilizes extended frames for larger messages. This CAN protocol is extremely useful for large vehicles used in transport, agriculture, and industrial settings. J1939 CAN Bus Network offer high-speed communication for faster execution of vital processes and faster analysis of microprocessor unit messages.
CANopen
CANopen is widely used to facilitate automation in manufacturing environments, featuring a highly configurable interface for any industrial application. These systems are resistant to harsh environments and require very little maintenance.
NMEA 2000
NMEA 2000 CAN bus devices are popular among marine applications. These systems allow data and power to be transmitted through single cable and offer high-speed communication between microprocessor units at up to 500 kilobytes per second.
See our blog post to learn all about CAN bus devices. To see how our capabilities can serve your needs, please contact us today.
Frequently Asked Questions
Which industries commonly use CAN Bus Devices?
Any product that goes on a vehicle and is powered by a 12V battery source.
How do I choose the right CAN Bus Device for my application?
Knowing the overview specification for your need will determine the type of device for your application. Contact us for assistance.
Can CAN Bus Devices be customized for specific applications?
Yes, based on the volume of the application.
What are the common features of SMP’s CAN Bus Devices?
Our CAN Bus Devices are fully sealed with robust packaging and minimal footprint.